L’usine du futur est en test sur le plateau de Saclay
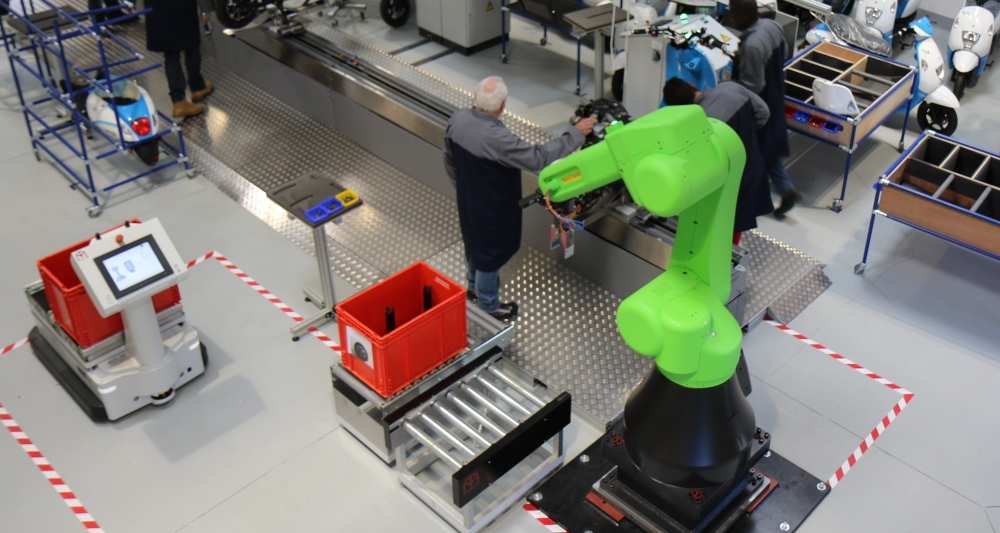
Elle est en test sur le plateau de Saclay. En créant un mini-site industriel avec 8 technologies embarquées connectées entre elles, le BCG préfigure ainsi l’Industrie 4.0.
Cloud, cyber sécurité, robotique avancée, impression 3D, réalité augmentée, internet industriel, Big Data, simulation numérique, intégration horizontale et verticale, pour le Boston Consulting Group (BCG), l’industrie est sur le point d’amorcer sa quatrième révolution grâce à ces huit technologies connectées entre elles. «Le modèle actuel est à bout de souffle, analyse le BCG. Depuis cinquante ans, les industriels misent sur les effets d’échelle, avec des usines toujours plus grandes, ultra-spécialisées. Les usines du futur seront plus agiles : avec le bon de productivité engendré, elles se relocaliseront pour se rapprocher de leur marché de destination».Contrairement aux idées reçues, l’usine du futur ne sera pas entièrement robotisée : « 8 % des tâches sont aujourd’hui automatisées. Nous estimons qu’avec l’industrie 4.0, ce taux passera à 25 %. Concernant les effectifs, nous pensons que la baisse se situera autour de 15 % par rapport aux effectifs actuels ». Les opérateurs resteront nécessaires, mais data scientists et consultants en cyber-sécurité devraient figurer au nombre des métiers les plus prisés par le secteur.
Tablette et logiciel de réalité virtuelle
Pour démonstration, le BCG a construit un modèle d’usine embarquant toutes ces technologies. Sur le plateau de Saclay, le cabinet de conseil en stratégie a lancé une opération inédite en France : il a aménagé en quelques mois un mini-showroom industriel, baptisé ICO (pour Innovation Center for Operations). Divisée en deux zones distinctes, l’usine fictive présente, dans la première, une ligne d’assemblage de scooters à monter et démonter en permanence. La seconde zone, consacrée à la production de bonbons, est présentée comme un modèle pour les industries de processus.Visuellement, c’est la ligne d’assemblage qui impressionne le plus. Une tablette équipée d’un logiciel de réalité virtuelle vérifie en quelques secondes que toutes les pièces de l’appareil sont bien présentes avant leur transport sur la ligne d’assemblage par un robot autonome. Les roues du scooter, elles, sont soulevées par un autre automate facile à programmer pour l’opérateur, qui le guide pour effectuer son premier geste. La configuration est ensuite sauvegardée dans la mémoire du robot afin qu’il puisse poursuivre sa tâche sans intervention humaine. « Demain, l’opérateur pourra programmer son robot en temps réel », anticipe-t-on au BCG. Coût de l’engin ? Entre 60.000 et 70.000 euros. Des prix qui ne cessent de baisser.
Personnalisation du produit en cours de production
Plus loin, sur la ligne d’assemblage, les opérateurs lisent aisément les informations stockées dans la puce RFID du scooter. En quelques secondes, ils connaissent la couleur du modèle désiré et les éventuelles options que le consommateur final souhaite ajouter. Dans ces usines agiles, la personnalisation ne se ferait donc plus en fin de chaîne mais au cours de la production. D’ici à quelques mois, le BCG annonce pouvoir à la fois des sèche-linge et des scooters, sur la même ligne de production. Si l’utilisation de ces technologies semble relativement aisée, le BCG concède que la difficulté réside dans la capacité à les connecter entre elles.
Une même chaîne de production pour 2 réalisations
De telles perspectives ouvrent la voie à de nouvelles stratégies d’industrialisation : deux petites entreprises, qui n’ont pas besoin de produire en continu, pourraient s’associer afin de rentabiliser leurs coûts de production. De même, une société pourrait plus facilement diversifier sa production en se servant de la même chaîne pour deux réalisations différentes. Surtout, les entreprises, qui n’auraient plus besoin de produire en série, chercheraient à se rapprocher davantage des consommateurs finaux, entraînant de fait un mouvement de réindustrialisation.De l’autre côté de la zone des scooters, la production de bonbons souligne l’importance des « data ». Température, pression, cadence, etc. sont autant de données de production analysées en permanence par un ordinateur, qui détermine ensuite quelles sont les conditions optimales pour améliorer tel ou tel paramètre de la production. « Le prix des capteurs a fortement baissé, ces dernières années, explique les consultants du BCG. Il faut compter 5 euros pour un capteur de proximité et 50 euros pour un capteur de température. La collecte de données est désormais accessible à tous les types d’entreprise ».Le BCG estime que le virage de l’industrie 4.0 pourrait se jouer au cours des 2 prochaines années. La Chine a déjà commandé 40 usines de ce type. Selon une de ses récentes étude*, près de trois quarts des industriels français indiquent être en phase de prise de conscience ou d’expérimentation vis-à-vis de l’industrie 4.0, soit un tout petit moins que les 78 % d’industriels allemands.(*) Etude BCG menée en juillet 2016 auprès de 322 managers français d’entreprises industriels de tous secteurs.Les Echos - 06/10/16
Prêts à développer une stratégie de Croissance Servicielle ?
Êtes-vous prêts à donner un nouvel élan à votre entreprise, à travers une approche orientée Services, une relation clients singulière et fidélisante, un modèle économique disruptif et en phase avec votre politique RSE, une politique managériale adaptée à toutes les générations, une performance commerciale revisitée et durable, et/ou des coopérations clients-fournisseurs-partenaires inédites et à forte valeur ajoutée ?
Chez Service&Sens, nous sommes là pour vous guider dans le développement de votre stratégie de croissance sur mesure, en transformant chacun de vos défis en opportunités concrètes, portées par vos équipes.
Abonnez-vous à Transform'Action News, notre newsletter incontournable !
En vous abonnant, vous aurez un accès privilégié à un monde d'avantages. Tous les deux mois, nous vous partagerons des contenus exclusifs, des analyses prospectives, des actualités de l'industrie, des conseils d'experts et bien plus encore.
Rejoignez notre communauté dynamique et enrichissante dès maintenant en vous abonnant à notre newsletter.
C'est rapide, facile et gratuit. Et souvenez-vous, l'information est le pouvoir.
D'autres articles sur le même sujet
Et cela ne saurait tarder !